SIGMA


For more than 50 years, this long-standing subsidiary of POMA has specialised in the design, manufacture and final assembly of cabins for passenger transport.
SIGMA’s know-how extends beyond a standard product catalogue. The company also designs and manufactures tailor-made cabins for the POMA Group’s special projects such as funiculars, APMs and observation wheel capsules.
Cabins that combine design, comfort and safety
Design
SIGMA’s Design Office uses a 3-D modelling tool to design both the standard range but also for special projects such as the London Eye capsules or the i360 platform.
SIGMA meets its commitments and its cabins blend perfectly into the project area, thanks to a very close match between the computer-generated images and the final product manufactured. Designers can see the carriers taking shape right before their eyes and are able to make the necessary improvements at all stages of production.
All over the world, SIGMA cabins are recognisable for their meticulous aesthetic design and their high level of safety. Passenger comfort, the reduction of noise and movement, the shape of the panoramic glass windows and the discretion of the safety components are some of the signature features of SIGMA carriers.
Production workshop
SIGMA manufactures many of the components of its cabins in its workshops, and thus controls the quality from manufacture to final assembly. This industrial choice guarantees the manufacturing quality and reliability of POMA products. Sturdiness, design and innovation…
These major assets are the fruit of the valuable expertise of its technicians, extensive experience, particularly suitable production equipment and rigorous and regular control operations.
Tailor-made cabins
SIGMA is able to design tailor-made and non-standard carriers whether for gondola or ropeway cabins, funicular railways, APMs or Ferris wheel capsules.
A cabin that blends into the landscape, a funicular with impressive panoramic glass windows and large-capacity panoramic capsules are all cabins designed and produced with a focus on modernity and elegance.
Body shop
With several spray booths at its disposal, SIGMA paints small-capacity cabins as well as very large funicular trains.
The continuous improvement of its high-precision processes and technologies enables SIGMA to guarantee superior product quality.
Carrier customisation
During assembly in the workshop, the carriers are customised according to the options chosen by the customer.
From the installation of heated seats to equipment for people with reduced mobility, to MTB carriers, including the creation of glass floors for a breath-taking panoramic effect in the cabins, air conditioning, on-board multimedia or the use of solar panels to make the cabins autonomous in terms of energy: the customisation of carriers matches the imagination of our customers and the ingenuity of our experts!
SIGMA key figures
1964
first “egg” cabin
60 years
of experience
135
employees
1979
POMA Group
more than 20 000
carriers manufactured
To design and produce high-quality vehicles in which passengers embark to fully enjoy their travel experience, it takes skilled and passionate individuals. Since our cabins have become a signature, the Sigma touch lies in capturing high standards and transforming them into the most faithful and refined creations.
If every second cable ropeway vehicle in the world comes out of our workshops in Northern Isère, it’s thanks to this unique expertise. Supported by a modern industrial site equipped with top-tier machinery for cutting, bending, welding, painting, and testing, we leverage cutting-edge techniques refined over 50 years. We also prioritize even the smallest details, from the aesthetics of a design to the meticulous comfort of an interior. As a result, each of our cabins and cable transport vehicles embodies reliability, innovation, and design.
At SIGMA, our CSR approach aligns with that of the Group. Sustainable mobility inevitably involves local sourcing and spans all our processes, with a deeply committed focus on environmental responsibility.
Sales and Services Director

Innovations & Performance
Diamond EVO cabins
Sigma has developed two new configurations; DIAMOND EVO cabins.
The Diamond cabin has been upgraded with improvements for both operators and end users: lighter cabs, simplified assembly, a standard height of 200 cm, adaptation to urban use, interior space reconfigured to offer options for both standing and sitting, sliding doors for easier boarding and space saving.
The EVO cabin is thus designed to adapt to multiple needs and operating environments while meeting the SIGMA quality standard.
Cabins with autonomous energy
Photovoltaic technology, integrated discreetly into the cabin, is now the main source of energy for cabins, and avoids having to charge the batteries in stations during the night. Smaller in size, the new generation photovoltaic panels are lighter while generating the same power, and easy to install. They offer a contemporary and innovative response to reduce the already low energy consumption of POMA ropeway transport solutions.
A partnership of elegance
Designed by Pinifarina, the Symphony cabins feature curves and angular or tapered shapes inspired by the automotive industry.
Attention to interior and exterior details gives the product its style and strengthens the corporate image.
Comfort, a challenge for SIGMA innovations
SIGMA carriers, used in a broad range of sectors such as mountains, urban mobility, tourism and leisure, are designed for everyday life, holidays or free time.
From the standard to the premium product, comfort represents a strong focus in the development of carriers to offer ever more modularity and well-being to passengers; this involves ergonomics, the choice and quality of materials, a series of options and a meticulous finish.
Sustainable investments
With the creation of a new storage space of more than 700 sq. m, we have been able to eliminate the cost of external storage and to limit our carbon footprint in transport to refocus our activities on our Veyrins site
Sigma

ICONIC PROJECTS

London Eye
Right in the heart of London, on the banks of the River Thames, 32 rotating capsules climb to 135 m, taking visitors above the rooftops of London for an exceptional view of the entire capital.
Learn more
Airtram New York
With the installation of this ultra-modern aerial tramway, POMA has provided New Yorkers with the most advanced technology in urban ropeway transportation. It is 960 m long and connects Roosevelt Island to Manhattan in just three minutes, passing over the East River in great comfort with unique views of New York through the huge windows on both cabins.
Learn more
La Daille
For the first time in France, in La Daille, a gondola lift with 57 10-seater Symphony cabins designed by Pininfarina offers maximum comfort to passengers.
Learn more
i360
POMA designed and manufactured the entire pod and drive system of the world’s tallest observation tower, known as the British Airways i360. A unique concept, located on the Brighton seafront in the south of England.
Learn moreCONTACT
3 place du Petit Veyrins – 38630 VEYRINS
DISCOVER OUR GROUP

SACMI
A subsidiary of the POMA Group since 1960, SACMI specialises in mechanical welding, machining, installation and assembly of mechanical sub-assemblies for ropeway transport systems.
Learn more
SEMER
SEMER, POMA’s subsidiary, specialises in the engineering and manufacturing of electrical equipment and industrial automation for ropeway transport systems. It is recognised worldwide for its know-how in electrical engineering, safety-instrumented systems, process control and industrial automation.
Learn moreSEMER


SEMER, POMA’s subsidiary, specialises in the engineering and manufacturing of electrical equipment and industrial automation for ropeway transport systems. It is recognised worldwide for its know-how in electrical engineering, safety-instrumented systems, process control and industrial automation.
SEMER, an undisputed leader in electrical engineering
Engineering
For more than 40 years, SEMER has been creating smart solutions to meet the safety and comfort requirements of operators and users of ropeway transport systems. SEMER engineering relies on the expertise in automation, electrical engineering and industrial IT of its passionate technicians and engineers.
Implementation
SEMER site managers and cable fitters, experienced in travelling to the five continents, install, wire and test onsite the equipment manufactured by SEMER. Their ability to work closely with local professionals, both in France and abroad, contributes to the smooth running of worksites, the quality of the installation and the satisfaction of the end customer.
Operation and Maintenance
SEMER engineers design software to aid in the diagnosis, troubleshooting and maintenance of POMA systems, while technicians provide training and assistance.
Innovation, SEMER’s watchword, is powered by cutting-edge digital technologies.
SEMER key figures
1979
Creation
ISO 9001
certified since 1994
110
employees
1991
Subsidiary of the POMA Group
175 000 hours
of design/production in 2019
SEMER’s growth is fuelled by its strong know-how, its human skills, and a solid partnership with its customers.
Our success is based on rational, competitive, reliable and innovative solutions. Meeting technological challenges is a necessary driver for improving our skills. Adapting our resources and our working methods to meet the needs of the markets, our customers and our employees is also a priority for SEMER.
CEO, SEMER

confort et performance d’exploitation
SmartBOARD, control and driving tool
SEMER was inspired by the varied needs of operators to develop the SmartBOARD, an intelligent, ergonomic and aesthetic control and driving tool for ropeway systems; the centralised functionalities and the precise information delivered allow greater responsiveness in decision-making, for redesigned operating and maintenance comfort; the essential objective remains, of course, the safety of users.
DirectDrive®, the virtuous motor
The DirectDrive motor owes its success to its simplicity and modularity. The drives are assembled and adjusted entirely by SEMER engineers.
DirectDrive technology offers multiple advantages: high availability, operating comfort and reduced maintenance, reduced environmental footprint and greater efficiency.
EcoDRIVE® function
Integrated into the ropeway driver’s station, EcoDRIVE mode automatically regulates the speed of the system according to the number of people who are about to use it. The setting is determined so as to ensure the comfort of passengers on-line, and an acceptable waiting time. For the operator, it generates significant energy savings.
ProTEC maintenance radio remote control
Approved by STRMTG and recognised by CARSAT, ProTEC is the ideal tool developed by SEMER to protect workers during maintenance operations in the vicinity of moving parts. ProTEC is the only radio remote control with positive safety (instantaneous shutdown of the installation if the trigger is released, ensuring worker protection in the event of a problem).
SEMER

Iconic Projects

Téléo
More than 8,000 passengers will board the cabins of the Téléo tricable ropeway every day. Part of the Toulouse Agglomeration’s transport network, it crosses a river and travels over a hill to link three major hubs of activity in the south of Toulouse: the University Cancer Institute, Rangueil Hospital and Paul Sabatier University.
Learn more
Miami Airport
Miami International Airport inaugurated its two APMs in 2016 and 2017. The two APM trains travel 375 m and carry up to 12,000 passengers per hour between the main terminal and terminal E.
Learn more
London Eye
Right in the heart of London, on the banks of the River Thames, 32 rotating capsules climb to 135 m, taking visitors above the rooftops of London for an exceptional view of the entire capital.
Learn moreContact
PAE du pays du Mont-Blanc – 74190 PASSY
Discover our group

COMAG
COMAG is POMA Group’s expert in the installation, inspection and maintenance of ropeway transport systems.
Learn more
SACMI
A subsidiary of the POMA Group since 1960, SACMI specialises in mechanical welding, machining, installation and assembly of mechanical sub-assemblies for ropeway transport systems.
Learn moreSACMI


A subsidiary of the POMA Group since 1960, SACMI specialises in mechanical welding, machining, installation and assembly of mechanical sub-assemblies for ropeway transport systems. A know-how developed in the heart of the Alps and an industrial structure commensurate with the most ambitious projects.
POMA therefore relies on the expertise of its subsidiary to deal with very specific requests such as the development of tri-cable ropeways for China, observation wheel capsules or even onshore wind turbines for the activity of POMA Leitwind! Thanks to its strategic position, SACMI is also the Group’s main logistics hub from which all equipment travels around the world to become iconic “Made in France” projects.
the mechanical welding expert of the Poma Group
Mechanical welding of ropeway transport sub-assemblies
For more than 60 years, SACMI has been producing metal parts for ropeway transport structures. The industrial mastery of the manufacturing processes (sheet metal making, manual and robot welding) allows SACMI to adapt to different request and to remain flexible in terms of deadlines and costs, while complying with demanding quality standards (SACMI is notably EN 1090 EXC4 and ISO 9001 certified).
Machining of specific components
SACMI is equipped with a machining centre to ensure optimal surface finish and geometry. The functionality and the level of safety of the parts processed on site are controlled from A to Z. Machining centres are able to handle small series of parts just as well as large custom components.
Installation and pre-assembly of mechanical sub-assemblies
SACMI’s assembly workshops produce mechanical sub-assemblies from mechanically-welded and machined structures.
Station modules, station structures, motor units, voltage units, sheaves and line elements for the Group's mono-cable and multi-cable systems are pre-assembled, adjusted, wired and tested in the workshop before being shipped to the site.
This work is carried out in collaboration with POMA teams and other subsidiaries in order to maximise the added value produced in the workshop and thus reduce exposure to the constraints of external sites.
The Group’s logistics platform
The SACMI logistics department manages the flow of parts for the Group. Its main missions are the unloading and inspection of goods, inventory management, preparation of components necessary for production, loading and shipping of components to subcontractors or to construction sites.
SACMI is the main logistics platform of the POMA Group.
SACMI key figures
150
employees
100 000 sq. m
of extended site
82 km
of manual welds
6 225 sq. m
of cut sheets
60
contracts per year
The Gilly-sur-Isère production facility operated by SACMI has been designed to optimise the POMA Group’s overall production chain, in particular by internalising highly technical processes and high added-value operations that were previously subcontracted. The site is equipped with welding robots, multi-axis machining centres, complex, specific large-scale sheet metal work, etc., providing the Group with unique know-how.
With the speeding-up of flows, the POMA Group is increasingly better placed to offer a comprehensive product range on a market where time-to-market is a key value.
By refocusing a large number of production activities for its components and mechanical assemblies, POMA demonstrates its commitment to eco-responsibility; by significantly decreasing the volume of transport between operators, the Group is reducing its CO2 emissions.
CEO of SACMI

« I have worked closely with SACMI for about twelve years. I was able to closely follow the technological optimisations undertaken, and more particularly on the new Gilly-sur-Isère site. SACMI has developed unique skills in sheet-metal working for large mechanically-welded parts, in the machining of large parts as well as in the mechanical assembly of all systems. The structure’s high level of agility allows us to develop quality solutions to the challenges of producing our ropeway systems in a competitive world. »
POMA Supply Chain Manager

a flagship innovation
The 5-part sheave is a major development for the industry. Sheaves are parts at the heart of the system and are used to drive the rope. They are manufactured entirely by SACMI (assembly, welding, machining, painting and mounting of the liner) and can measure up to 6 metres in diameter.
The 5-part sheave consists of a hub and 4 quarter sheaves, which are assembled on site. This innovation optimises the possibilities of packaging, transport and handling of the equipment until it is installed on site during the construction phase.
Made in France
As part of its social commitment, SACMI regularly organises site visits to promote the “Made in France” industry and its unique know-how.
Last year, SACMI had the pleasure of welcoming:
- Students from engineering and management schools, vocational high schools,
- Professionals from the region, the sector, business associations including Talents Féminins de Savoie,
- Customers and delegations
iconic projects

Téléo
More than 8,000 passengers will board the cabins of the Téléo tricable ropeway every day. Part of the Toulouse Agglomeration’s transport network, it crosses a river and travels over a hill to link three major hubs of activity in the south of Toulouse: the University Cancer Institute, Rangueil Hospital and Paul Sabatier University.
Learn more
Miami Airport
Miami International Airport inaugurated its two APMs in 2016 and 2017. The two APM trains travel 375 m and carry up to 12,000 passengers per hour between the main terminal and terminal E.
Learn more
Ain Dubai
For the world’s largest observation wheel, commissioned for the Dubai World Expo, POMA built 48 outsized capsules, the largest and heaviest ever produced. The teams came up with evermore ingenious product development solutions and met a very high level of customer demand.
Learn moreCONTACT
396, route des Chênes – 73200 GILLY-SUR-ISERE – FRANCE
Discover our group

COMAG
COMAG is POMA Group’s expert in the installation, inspection and maintenance of ropeway transport systems.
Learn more
SIGMA
For more than 50 years, this long-standing subsidiary of POMA has specialised in the design, manufacture and final assembly of cabins for passenger transport. SIGMA’s know-how extends beyond a standard product catalogue. The company also designs and manufactures tailor-made cabins for the POMA Group’s special projects such as funiculars, APMs and observation wheel capsules.
Learn moreCOMAG

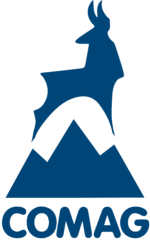
COMAG is POMA Group’s expert in the installation, inspection and maintenance of ropeway transport systems.
Its wide range of expertise and services, proven in demanding environments, gives it unique know-how and complete proficiency in the operations deployed on all POMA sites, all over the world. This know-how, acquired by COMAG in the Alps, is now channelled into large-scale infrastructure projects, or the maintenance of tourist infrastructure and amusement parks
SEMER, an undisputed leader in electrical engineering
Engineering
For more than 40 years, SEMER has been creating smart solutions to meet the safety and comfort requirements of operators and users of ropeway transport systems. SEMER engineering relies on the expertise in automation, electrical engineering and industrial IT of its passionate technicians and engineers.
Implementation
SEMER site managers and cable fitters, experienced in travelling to the five continents, install, wire and test onsite the equipment manufactured by SEMER. Their ability to work closely with local professionals, both in France and abroad, contributes to the smooth running of worksites, the quality of the installation and the satisfaction of the end customer.
Operation and Maintenance
SEMER engineers design software to aid in the diagnosis, troubleshooting and maintenance of POMA systems, while technicians provide training and assistance.
Innovation, SEMER’s watchword, is powered by cutting-edge digital technologies.
SEMER key figures
1979
Creation
ISO 9001
certified since 1994
110
employees
1991
Subsidiary of the POMA Group
175 000 hours
of design/production in 2019
At a time when safety issues challenge project managers, operators, communities and users, we are enriching the value of the POMA Group’s offer, capitalizing on our decades of experience and backed by a solid logic of continuous improvement.
In addition to unique know-how in the maintenance of strategic parts of the cable transport system, we have now achieved the highest level of overall site control:
- • We analyze and take into account environmental issues, material and human risks in natural and urban environments
- • Our ranges and intervention procedures are pre-defined and constantly improved
- • We systematically draft and apply prevention plans regardless of the operation
Beyond the strictest respect for French and European standards, we deploy our processes throughout the world, with teams of business experts, also knowing how to interface with local partners to maintain a maximum level of quality. Our vision: to continue to be the world reference for construction sites in hostile or demanding environments!
COMAG President

COMAG’s commitment
All operations are carried out in strict compliance with environmental requirements. Illustrations include the decision to pre-assemble sub-equipment prior to the start of work, in order to limit transportation and operations on site.
A commitment shared across the POMA group.
Iconic Projects

Téléo
More than 8,000 passengers will board the cabins of the Téléo tricable ropeway every day. Part of the Toulouse Agglomeration’s transport network, it crosses a river and travels over a hill to link three major hubs of activity in the south of Toulouse: the University Cancer Institute, Rangueil Hospital and Paul Sabatier University.
Learn more
Miami Airport
Miami International Airport inaugurated its two APMs in 2016 and 2017. The two APM trains travel 375 m and carry up to 12,000 passengers per hour between the main terminal and terminal E.
Learn more
London Eye
Right in the heart of London, on the banks of the River Thames, 32 rotating capsules climb to 135 m, taking visitors above the rooftops of London for an exceptional view of the entire capital.
Learn moreContact
PAE du pays du Mont-Blanc – 74190 PASSY